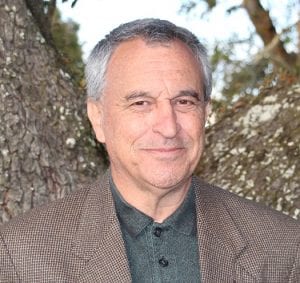
Mark Isaacs is joking, a little, when he says the WonderWindow has been fifty years in the making. But that’s the length of his career as a Massachusetts Institute of Technology trained architect who became a developer of award-winning “green” buildings, now turned start-up entrepreneur. Isaacs doesn’t just want to innovate the way windows are made and installed in walls—but perhaps even how they are manufactured and distributed.
Isaacs and his wife moved to Bay St. Louis, Miss., after the Great Recession of 2009. Before that, they were the developers of Legacy Lofts, an 84,000-square-foot, mixed-use, 4-1/2 story building with 38 condos plus retail space in Louisville, Kentucky. The building won the “2008 Green Multifamily Building of the Year” award from the National Association of Homebuilders. It used geothermal heating and cooling and super-insulation to get estimated utility bills for each condo down to an astounding $10 per month.
The panic hit, and Isaacs’ bank sold to another bank. The first day he could finally sit down with that bank’s president was September 15, 2008, the same day the Lehman Brothers investment bank declared bankruptcy in the largest filing in U.S. history. The Dow Jones then had its biggest drop since September 11, 2001—and banks put development projects across the country on hold, including Legacy Lofts.
“Suddenly, when I didn’t have a payroll to meet for 30 plus employees and 200 subcontractors, I was free to think about those things I thought of as an MIT student,” Isaacs said. Two patents later, he said, he had fascinating ideas for the future of solar energy and ways to store it under buildings for space heating and cooling—but they’re complicated technologies that don’t yet lend themselves to commercialization.
Thinking more practically brought him back to windows. “I’ve been fiddling with windows in one form or another for about six years,” he said, noting that he got a Mississippi Seed Fund award early on from Innovate Mississippi that helped finance his work on early prototypes of the WonderWindow.
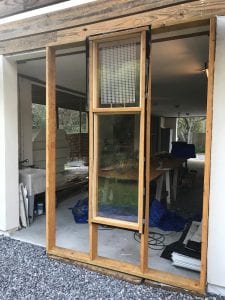
From 2014-2018, he progressed through five different prototypes, and then just as many in quick succession in 2019. Five more iterations in the first six months of 2020 have continued the progress. In September, he’ll start a federal Small Business Innovation Research, or SBIR, grant to finalize, test and certify the windows as he moves toward commercialization.
Each WonderWindow is a multi-paned, acrylic window with two to three times the efficiency of today’s state-of-the-art windows, but at a comparable cost. A big chunk of the innovation comes with the window’s frame; Isaacs’ design eliminates material that can be highly energy-inefficient.
“When you eliminate six square feet of framing around the window, and several added square feet of window sash and frame, you are essentially doubling the efficiency of walls and windows at the same cost of conventional construction,” he said. “If we’re successful in demonstrating that, there’s a chance that we’ll change the way homes are built nationwide.”
That’s not all Isaacs wants to change—he also plans an innovative distribution model. Instead of having one large manufacturing facility that ships ready-made windows worldwide, he designed the windows so that modestly skilled workers can make and deliver them in their local markets. That approach will also cut down on the greenhouse gases expended.
As he works to take the WonderWindow to market this year, he said Innovate Mississippi has been there to help him fund his research and connect him to other vital resources in the state.
“I can’t say enough about Innovate Mississippi,” Isaacs said, “At this point, they’re almost all we have in terms of generating a statewide innovation ecosystem … along with our universities. Innovate’s MS Fast program has been instrumental in assisting with our two SBIR grant successes. Hats off to Tony Jeff and Joe Graben for their assistance.”
This summer, a team of mid-career students in Mississippi State University’s online MBA program used his company for their capstone project. Isaacs’ said he was thrilled with the results, as the team helped him develop a go-to-market strategy focusing on eight target markets. The team concluded these early-adopter markets could yield over $20 million in revenue in six years.
Isaacs counts Buckminster Fuller (whom he saw speak 50 years ago) as an inspirational figure, particularly his lesson that “The best way to predict the future is to design it.”
Thomas Edison is another role model. In 1931, Edison said: “I’d put my money on the sun and solar energy; what a source of power.” Isaacs believes that in 2020 we can work toward affordable net-zero energy buildings, including rooftop solar, through a few improvements to the ways we build walls and windows.
He also channels Edison when offering his advice to other entrepreneurs.
“You’ve got to stick with it, yet know when an idea will not be actionable or investible,” he said. “Make failure your friend. The quicker you fail—as in the improvements that come through rapid, iterative prototyping—the quicker you’ll get to success.”
Isaacs expects to complete testing and code certification this year, and would like to talk to interested builders and architects about low-rise, wood-frame demonstration buildings in the planning stages for early 2021.
Top image: While earlier prototypes used wood or PVC for the window sash, the latest WonderWindows effectively eliminate sash material. Here, a six-pane prototype offers clarity of view and edge-to-edge R7 thermal resistance, more than double the overall thermal resistance of conventional windows.